Anda seorang pemilik perusahaan? Kuncinya terus evaluasi seluruh kekurangan dan memperbaiki diri.
(Belajar dari Toyota ways)
Apa itu Toyota Way? Toyota Way merupakan filosofi atau pedoman/prinsip manajemen yang diberlakukan di perusahaan Toyota secara menyeluruh. Filosofi ini meliputi berbagai hal termasuk Toyota Production System (sistem produksi Toyota).
ADVERTISEMENT
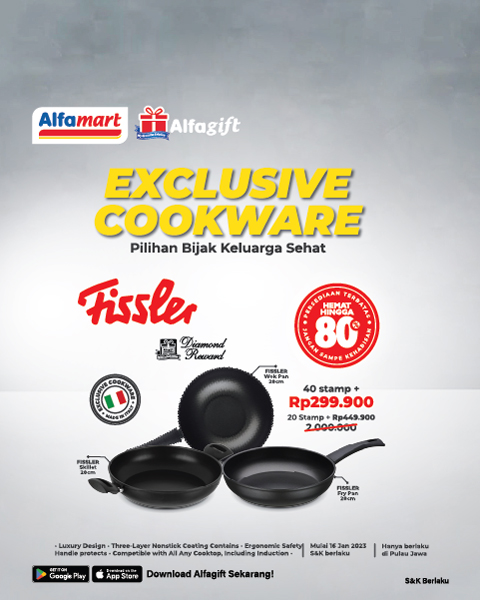
SCROLL TO RESUME CONTENT
Ada 14 prinsip dasar yang ada di dalam filosofi ini.
Tentunya, filosofi ini tidak berkaitan dengan investasi mudah karena memang skala dari filosofi ini adalah untuk perusahaan level internasional.
Berikut penjelasan 14 prinsip The Toyota Way yang terbagi dalam beberapa bagian.
- Filosofi Jangka Panjang (Bagian I):
Prinsip 1: Prinsip Toyota Way yang pertama adalah terkait dengan keputusan. Keputusan manajemen didasarkan pada filosofi jangka panjang walau harus mengorbankan keuangan jangka pendek.
Dari sini bisa dilihat bahwa yang menjadi fokus Toyota adalah perjalanan dan hasil untuk jangka panjang yang lebih penting dari hasil jangka pendek. Dengan demikian, perusahaan akan terus berkembang.
- Proses Benar Memberikan Hasil Benar (Bagian II)
Prinsip 2: Menciptakan sebuah proses yang berkelanjutan sehingga akan mengangkat semua permasalahan ke permukaan.
Toyota memang selalu menciptakan proses kerja yang berkelanjutan sehingga tidak ada waktu kosong (idle). Bila perlu proses kerja yang ada akan didesain ulang agar bisa melihat permasalahan apa yang terjadi.
Prinsip 3: Menggunakan sistem “tarik” (pull) agar produksi tidak berlebih.
Berikan pelanggan dengan apa yang mereka inginkan pada saat waktu yang mereka butuhkan serta dengan jumlah yang sesuai dengan kebutuhan mereka.
Prinsip 4: Meratakan beban kerja (heijunka), berkejalah layaknya seekor kura-kura dan tidak seperti seekor kelinci.
Semua beban kerja akan diratakan kepada setiap sumber daya yang ada. Biar lambat, semua beban terselesaikan dengan baik.
Prinsip 5: Membangun budaya untuk berhenti memperbaiki masalah dengan demikian maka kualitas terbaik akan diperoleh dari awal.
Bagi pelanggan, kualitas adalah nomor satu. Oleh sebab itu, hindari kebiasaan untuk memperbaiki masalah dimana hal ini akan membuat kualitas terbaik dari awal produksi.
Prinsip 6: Tugas dan proses terstandar adalah sebuah pondasi untuk melakukan perbaikan secara berkelanjutan dan untuk pemberdayaan karyawan.
Metode yang sudah terbukti stabil bisa digunakan terus secara berulang-ulang tanpa melupakan aspek perbaikan jika dibutuhkan sehingga dari mulai tugas, proses dan kemampuan karyawan akan terus menjadi baik.
Prinsip 7: Menggunakan pengendalian secara visual sehingga tidak akan ada masalah tersembunyi.
Indikator yang dapat divisualkan secara sederhana akan membantu semua komponen menyelesaikan tugas dan masalahnya. Prinsip yang menyimpang dari filosofi akan mudah diketahui.
Prinsip 8: Hanya menggunakan teknologi handal yang sudah teruji guna melayani semua orang dan proses.
Ya, hanya menggunakan teknologi terpercaya dan teruji untuk membantu semua orang serta membantu proses yang ada.
- Menambah Nilai Perusahaan Dengan Cara Mengembangkan Orang Serta Mitra Kerja (Bagian III)
Prinsip 9: Mengembangkan seorang pemimpin untuk benar-benar memahami tugas atau pekerjaannya, menjiwai secara dalam filosofi yang sudah ditetapkan, dan mengajarkannya kepada yang lain.
Lebih baik untuk mengembangkan pemimpin dari dalam perusahaan sendiri bukan dengan cara mendatangkan dari luar. Tentu hal ini lebih baik dilihat dari banyak hal.
Prinsip 10: Mengembangkan orang dan tim yang memiliki kemampuan luar biasa yang bisa menganut filosofi perusahaan.
Budaya dan sistem yang kuat serta stabil akan membuat seluruh sumber daya manusia menjiwai dan mengikutinya. Selanjutnya, latih diantara mereka yang memiliki kemampuan luar biasa untuk dikembangkan lebih maju.
Prinsip 11: Hormati atau respek kepada jaringan mitra serta pemasok Anda dengan cara memberikan mereka tantangan baru serta membantunya untuk melakukan peningkatan.
Ya, menghormati mitra dan pemasok adalah kewajiban, namun dengan cara memberi mereka tantangan yang akan membuat mereka melakukan peningkatan.
- Menyelesaikan Akar Permasalahan Secara Terus-Menerus Untuk Mendorong Pembelajaran Organisasi (Bagian IV)
Prinsip 12: Turun langsung untuk melihat sendiri situasi dan kondisi sebenarnya (genchi genbutsu).
Prinsip 13. Mengambil keputusan dengan perlahan dengan cara konsensus, serta seksama dalam mempertimbangkan pilihan dan implementasikan atau menerapkan keputusan secara cepat (nemawashi).
Prinsip 14. Menjadi sebuah perusahaan pembelajar dengan cara refleksi pada diri secara terus menerus (hansei) serta peningkatan yang berkesinambunganda (kaizen).
Seluruh 14 prinsip ini sudah menjadi kunci utama bagaimana Toyota dan Lexus terus berkembang menjadi yang terbaik di pasar internasional.
Apakah anda juga sang pemilik perusahaan bakalan memiliki way of solve problem sendiri? Terus membangun dan memperbaiki diri itu kunci yang utama.
The secret of Toyota ways
Diambil dari web resmi Toyota, https://global.toyota/en/company/vision-and-philosophy/production-system/ Sebuah sistem produksi berdasarkan filosofi mencapai penghapusan lengkap semua limbah dalam mengejar metode yang paling efisien.
Sistem produksi kendaraan Toyota Motor Corporation adalah cara membuat sesuatu yang kadang-kadang disebut sebagai “sistem manufaktur ramping”, atau “sistem Just-in-Time (JIT)”, dan telah menjadi terkenal dan dipelajari di seluruh dunia.
Sistem kontrol produksi ini didirikan berdasarkan perbaikan terus-menerus selama bertahun-tahun, dengan tujuan membuat kendaraan yang dipesan oleh pelanggan dengan cara tercepat dan paling efisien, untuk mengirimkan kendaraan secepat mungkin.
Sistem Produksi Toyota (TPS) didirikan berdasarkan dua konsep: “jidoka” (yang dapat diterjemahkan secara bebas sebagai “otomatisasi dengan sentuhan manusia”), seperti ketika terjadi masalah, peralatan segera berhenti, mencegah produk cacat diproduksi. ; dan konsep “Just-in-Time”, di mana setiap proses hanya menghasilkan apa yang dibutuhkan untuk proses selanjutnya dalam aliran yang berkesinambungan.
Berdasarkan filosofi dasar jidoka dan Just-in-Time, TPS dapat secara efisien dan cepat menghasilkan kendaraan dengan kualitas suara, satu per satu, yang sepenuhnya memenuhi kebutuhan pelanggan.
TPS dan pendekatannya terhadap pengurangan biaya adalah sumber kekuatan kompetitif dan keunggulan unik bagi Toyota. Mengasah kekuatan ini secara menyeluruh sangat penting untuk kelangsungan hidup Toyota di masa depan. Kami akan menggunakan inisiatif ini dan mengembangkan sumber daya manusia kami untuk membuat mobil yang lebih baik yang akan dihargai oleh pelanggan.
Konsep TPS
Bagi Toyota, jidoka berarti mesin harus berhenti dengan aman setiap kali terjadi kelainan. Oleh karena itu, mencapai jidoka membutuhkan pembangunan dan peningkatan sistem dengan tangan sampai dapat diandalkan dan aman. Pertama, insinyur manusia dengan cermat membangun setiap komponen lini baru dengan tangan untuk memenuhi standar, kemudian, melalui kaizen tambahan (perbaikan berkelanjutan), terus menyederhanakan operasinya.
Akhirnya, nilai tambah oleh operator manusia jalur tersebut menghilang, artinya operator mana pun dapat menggunakan jalur tersebut untuk menghasilkan hasil yang sama. Baru kemudian mekanisme jidoka dimasukkan ke dalam jalur produksi yang sebenarnya.
Melalui pengulangan proses ini, mesin menjadi lebih sederhana dan lebih murah, sementara perawatan menjadi lebih sedikit memakan waktu dan lebih murah, memungkinkan pembuatan jalur yang sederhana, ramping, fleksibel yang dapat beradaptasi dengan fluktuasi volume produksi.
Pekerjaan yang dilakukan dengan tangan dalam proses ini adalah dasar dari keterampilan teknik. Mesin dan robot tidak berpikir sendiri atau berevolusi sendiri. Sebaliknya, mereka berkembang saat kami mentransfer keterampilan dan keahlian kami kepada mereka.
Dengan kata lain, pengerjaan dicapai dengan mempelajari prinsip-prinsip dasar manufaktur melalui pekerjaan manual, kemudian menerapkannya di lantai pabrik untuk terus melakukan perbaikan. Siklus peningkatan keterampilan manusia dan teknologi ini adalah inti dari jidoka Toyota. Memajukan jidoka dengan cara ini membantu memperkuat daya saing manufaktur dan pengembangan sumber daya manusia kami.
Kebijaksanaan dan kecerdikan manusia sangat diperlukan untuk memberikan mobil yang lebih baik kepada pelanggan. Kedepannya, kami akan mempertahankan dedikasi teguh kami untuk terus mengembangkan sumber daya manusia yang dapat berpikir mandiri dan menerapkan kaizen.
Prinsip Dasar Jidoka
Operator memberi sinyal malfungsi
Kerusakan ditandai melalui “andon” (papan tampilan masalah)
Tepat waktu/ just in time
Meningkatkan produktivitas― Membuat hanya “apa yang dibutuhkan, ketika dibutuhkan, dan dalam jumlah yang dibutuhkan”
Memproduksi produk berkualitas secara efisien melalui penghapusan lengkap pemborosan, inkonsistensi, dan persyaratan yang tidak masuk akal pada lini produksi (dikenal masing-masing dalam bahasa Jepang sebagai muda, mura, muri).
Untuk memenuhi pesanan dari pelanggan secepat mungkin, kendaraan dibuat secara efisien dalam waktu sesingkat mungkin dengan mengikuti hal-hal berikut:
- Ketika pesanan kendaraan diterima, instruksi produksi harus dikeluarkan ke awal jalur produksi kendaraan sesegera mungkin.
- Jalur perakitan harus diisi dengan jumlah semua suku cadang yang diperlukan sehingga semua jenis kendaraan yang dipesan dapat dirakit.
- Jalur perakitan harus mengganti suku cadang yang digunakan dengan mengambil jumlah suku cadang yang sama dari proses produksi suku cadang (proses sebelumnya).
- Proses sebelumnya harus ditebar dengan jumlah kecil dari semua jenis suku cadang dan hanya menghasilkan jumlah suku cadang yang diambil oleh operator dari proses berikutnya.
Asal Sistem Produksi Toyota Sistem produksi yang disempurnakan dari generasi ke generasi
Akar Sistem Produksi Toyota
Sistem Produksi Toyota (TPS), yang didasarkan pada filosofi penghapusan total semua pemborosan dalam mengejar metode yang paling efisien, memiliki akar menelusuri kembali ke alat tenun otomatis Sakichi Toyoda.
TPS telah berkembang melalui bertahun-tahun trial and error untuk meningkatkan efisiensi berdasarkan konsep Just-in-Time yang dikembangkan oleh Kiichiro Toyoda, pendiri (dan presiden kedua) Toyota Motor Corporation.
Pemborosan dapat bermanifestasi sebagai persediaan berlebih, langkah pemrosesan yang tidak relevan, dan produk cacat, di antara contoh lainnya. Semua elemen “limbah” ini saling terkait satu sama lain untuk menghasilkan lebih banyak limbah, yang pada akhirnya berdampak pada manajemen korporasi itu sendiri.
Alat tenun otomatis yang ditemukan oleh Sakichi Toyoda tidak hanya membuat pekerjaan otomatis yang dulunya dilakukan secara manual, tetapi juga membangun kemampuan untuk membuat penilaian ke dalam mesin itu sendiri. Dengan menghilangkan produk cacat dan praktik pemborosan terkait, Sakichi berhasil meningkatkan produktivitas dan efisiensi kerja dengan cepat.
Kiichiro Toyoda, yang mewarisi filosofi ini, mulai mewujudkan keyakinannya bahwa “kondisi ideal untuk membuat sesuatu tercipta ketika mesin, fasilitas, dan manusia bekerja sama untuk menambah nilai tanpa menghasilkan pemborosan.” Dia menyusun metodologi dan teknik untuk menghilangkan pemborosan antar operasi, antara lini dan proses. Hasilnya adalah metode Just-in-Time.
Melalui filosofi “Perbaikan Harian” dan “Pemikiran Baik, Produk Bagus, TPS telah berkembang menjadi sistem produksi yang terkenal di dunia. Bahkan saat ini, semua divisi produksi Toyota membuat perbaikan TPS siang dan malam untuk memastikan evolusinya yang berkelanjutan.
Semangat Toyota dari monozukuri (membuat sesuatu) sekarang disebut sebagai “Toyota Way”. Ini telah diadopsi tidak hanya oleh perusahaan di Jepang dan dalam industri otomotif, tetapi dalam kegiatan produksi di seluruh dunia, dan terus berkembang secara global.
Sakichi Toyoda (1867-1930), Toyoda Power Loom dilengkapi dengan perangkat penghenti otomatis pemutus pakan baru (dikembangkan pada tahun 1896)
Alat tenun otomatis pertama di dunia dengan gerakan bolak-balik tanpa henti, Type-G Toyoda Automatic Loom (dikembangkan pada tahun 1924)
Kiichiro Toyoda (1894-1952), Berdasarkan pengalamannya dalam memperkenalkan metode produksi aliran menggunakan konveyor rantai ke dalam jalur perakitan pabrik tekstil (selesai pada tahun 1927) dengan kapasitas produksi bulanan 300 unit, Kiichiro Toyoda juga memperkenalkan metode ini ke dalam lini produksi bodi di Toyota Motor. Pabrik Koromo Co., Ltd. (sekarang Pabrik Honsha), selesai pada tahun 1938.
Eiji Toyoda (1913-2013), Dengan memastikan penerapan jidoka dan metode Just-in-Time secara menyeluruh, Eiji Toyoda meningkatkan produktivitas pekerja dengan menambahkan nilai dan mewujudkan Sistem Produksi Toyota, yang memungkinkan Toyota bersaing langsung dengan perusahaan di Eropa dan AS.
Taiichi Ohno (1912-1990), dengan dukungan kuat dari Eiji Toyoda, Taiichi Ohno membantu membangun Sistem Produksi Toyota, dan membangun fondasi bagi semangat Toyota untuk “membuat sesuatu” dengan, misalnya, menciptakan kerangka dasar untuk metode Just-in-Time.
Bidodata Penulis Selengkapnya di https://www.linkedin.com/in/elpy-sariwanodja-64592b41/